Kod QR
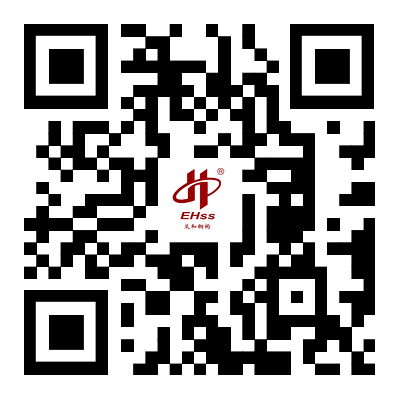
Produkty
Skontaktuj się z nami
Telefon
E-mail
Adres
Nr 568, Yanqing First Class Road, Jimo High-Tech Zone, Qingdao City, Shandong Prowince, Chiny
Budynek inżynieryjny o konstrukcji stalowejnazywany jest zielonym projektem XXI wieku, konstrukcja stalowa ma wiele zalet, takich jak wysoka wytrzymałość, duża nośność, niewielka waga, niewielka objętość zajmowanej przestrzeni, łatwa produkcja i montaż komponentów, oszczędność drewna itp., dlatego jest coraz szerzej stosowane w budynkach przemysłowych i cywilnych. Budynki o konstrukcji stalowej i Magazyny o konstrukcji stalowej są wszędzie.
Wraz z szybkim rozwojem przemysłu, stopniowo pojawiała się odporność stali na korozję oraz słaba odporność na rdzę i korozję oraz inne problemy, szczególnie na obszarach przybrzeżnych, a przemysł chemiczny stał się znaczącym problemem!
Korozja konstrukcji stalowej powoduje nie tylko straty ekonomiczne, ale także ukryte zagrożenie dla bezpieczeństwa konstrukcji, a wypadki inżynieryjne spowodowane korozją stali są powszechne, dlatego zabezpieczenie antykorozyjne konstrukcji stalowej (zwłaszcza cienkościennych elementów stalowych) jest wskazane o dużym znaczeniu gospodarczym i społecznym, a poniżej znajdują się wstępy i dyskusje dotyczące problemów występujących w procesie budowy i niektórych metod leczenia.
1. Główne przyczyny korozji konstrukcji stalowych
Zapobieganie korozji stali zaczyna się od zrozumienia przyczyn korozji stali.
1.1 Mechanizm korozji stali w temperaturze pokojowej (poniżej 100°C)
Korozja stali w temperaturze pokojowej to głównie korozja elektrochemiczna. Konstrukcje stalowe eksploatowane są w atmosferze w temperaturze pokojowej, a stal ulega korozji pod wpływem wilgoci, tlenu i innych zanieczyszczeń (nieoczyszczony żużel spawalniczy, warstwa rdzy, zabrudzenia powierzchniowe) znajdujących się w atmosferze. Wilgotność względna atmosfery jest niższa niż 60%, korozja stali jest bardzo niewielka; ale gdy wilgotność względna wzrasta do określonej wartości, szybkość korozji stali nagle wzrasta i wartość tę nazywa się wilgotnością krytyczną. W temperaturze pokojowej ogólna wilgotność krytyczna stali wynosi od 60% do 70%.
Kiedy powietrze jest zanieczyszczone lub zawiera sól w obszarach przybrzeżnych, wilgotność krytyczna jest bardzo niska, a na stalowej powierzchni łatwo tworzy się film wodny. W tym czasie żużel spawalniczy i nieobrobiona warstwa rdzy (tlenek żelaza) stanowią katodę, a elementy konstrukcji stalowej (materiał bazowy) jako anoda w warstwie wodnej korozji elektrochemicznej. Wilgoć atmosferyczna zaadsorbowana na powierzchni stali, tworząc warstwę wody, jest czynnikiem decydującym o korozji stali; Wilgotność względna atmosfery oraz zawartość zanieczyszczeń są ważnymi czynnikami wpływającymi na stopień korozji atmosferycznej.
1.2 Mechanizm korozji stali w wysokiej temperaturze (powyżej 100℃)
Korozja stali w wysokich temperaturach to głównie korozja chemiczna. W wysokiej temperaturze woda występuje w stanie gazowym, efekt elektrochemiczny jest bardzo mały, zredukowany do czynnika wtórnego. Kontakt metalu i suchego gazu (takiego jak O2, H2S, SO2, Cl2 itp.), powstawanie na powierzchni odpowiednich związków (chlorki, siarczki, tlenki), powstawanie korozji chemicznej stali.
2 Metody zabezpieczenia antykorozyjnego konstrukcji stalowych
Zgodnie z elektrochemiczną zasadą korozji stali, jeśli zapobiega się tworzeniu się baterii korozyjnej lub ją niszczy lub procesy katodowe i anodowe są silnie zablokowane, można zapobiec korozji stali. Stosowanie metody warstwy ochronnej w celu zapobiegania korozji konstrukcji stalowej jest obecnie powszechną metodą, powszechnie stosowaną warstwą ochronną są następujące rodzaje:
2.1 Metalowa warstwa ochronna: metalowa warstwa ochronna to metal lub stop o działaniu ochronnym katodowym lub anodowym, poprzez galwanizację, powlekanie natryskowe, powlekanie chemiczne, powlekanie na gorąco i powlekanie przesiąkowe oraz innymi metodami, konieczność zabezpieczenia powierzchni metalu w celu utworzenia metalowej warstwy ochronnej (folii) w celu odizolowania metalu od środowiska korozyjnego stykającego się z czynnikiem korozyjnym lub zastosowanie elektrochemicznego efektu ochronnego zabezpieczenia metalu, aby zapobiec korozji.
2.2 Warstwa ochronna: metodami chemicznymi lub elektrochemicznymi, aby powierzchnia stali wytworzyła odporną na korozję warstwę złożoną, w celu odizolowania ośrodka korozyjnego od kontaktu z metalem, aby zapobiec korozji metalu.
2.3 Niemetalowa warstwa ochronna: farbami, tworzywami sztucznymi, emalią i innymi materiałami, poprzez malowanie i natryskiwanie oraz innymi metodami, aby utworzyć warstwę ochronną na powierzchni metalu, tak aby metal i czynniki korozyjne odizolowały się, aby zapobiec korozji metalu .
3. Obróbka powierzchni stali
Podczas obróbki stali w fabryce powierzchnia elementów nieuchronnie będzie poplamiona olejem, wilgocią, kurzem i innymi zanieczyszczeniami, a także obecnością zadziorów, tlenku żelaza, warstwy rdzy i innych wad powierzchniowych. Z poprzednich głównych przyczyn korozji konstrukcji stalowych wiemy, że zawartość zanieczyszczeń jest ważnym czynnikiem wpływającym na stopień korozji atmosferycznej, a zanieczyszczenia powierzchniowe poważnie wpływają na przyczepność powłok na powierzchni stali i powodują, że farba warstwa pod korozją nadal się rozszerza, powodując uszkodzenie lub uszkodzenie powłoki, uniemożliwiając osiągnięcie pożądanego efektu ochronnego. Dlatego jakość obróbki powierzchni stali wpływa na działanie ochronne powłoki i trwałość oddziaływania, czasem nawet bardziej niż na samą powłokę, należy podkreślić różnorodne różnice w działaniu pod wpływem następujących aspektów:
3.1. W przypadku elementów nośnych, które są trudne do naprawy w okresie serwisowym, należy odpowiednio zwiększyć stopień odkamieniania.
3.2. Przed i po odkamienianiu należy dokładnie usunąć tłuszcz, zadziory, skórkę lekarską, rozpryski i tlenek żelaza.
3.3. Odbiór jakościowy prac odkamieniania i malowania będzie zgodny z przepisami.
4. Powłoka antykorozyjna
Powłoki antykorozyjne składają się zazwyczaj z podkładu i powłoki nawierzchniowej. Podkład w proszku więcej, mniej materiału bazowego, warstwa szorstka, funkcją podkładu jest nadanie powłoce farby na poziomie oddolnym i połączeniu powłoki nawierzchniowej o konsystencji stałej, to znaczy o dobrej przyczepności; podkład zawiera pigmenty hamujące korozję, może zapobiegać powstawaniu korozji, a niektóre mogą również służyć do pasywacji metalu i ochrony elektrochemicznej, aby zapobiec rdzewieniu metalu. Warstwa nawierzchniowa składa się z mniej proszku, więcej materiału bazowego, po uzyskaniu połysku główną funkcją jest ochrona dolnej warstwy podkładu, dlatego powinna być nieprzepuszczalna dla atmosfery i wilgoci oraz powinna być odporna na rozkład fizyczny i chemiczny spowodowane wietrzeniem. Obecnym trendem jest stosowanie żywic syntetycznych w celu poprawy odporności medium na warunki atmosferyczne. Powłoki antykorozyjne odporne na warunki atmosferyczne są z reguły odporne jedynie na korozję w fazie gazowej w atmosferze. W miejscach narażonych na korozję powodowaną przez kwasy, zasady i inne media należy stosować powłoki odporne na działanie kwasów i zasad.
Farby antykorozyjne ze względu na funkcję ochronną można podzielić na farbę podkładową, farbę środkową i warstwę wierzchnią, każda warstwa farby ma swoje własne cechy, z których każda odpowiada na własną odpowiedzialność, kombinację warstw, tworzenie powłoki kompozytowej poprawić działanie antykorozyjne, przedłużyć żywotność.
podkłady 4.1
Warstwa podkładowa Powszechnie stosowane powłoki antykorozyjne to podkład bogaty w cynk i podkład epoksydowo-żelazowo-czerwony. Farba bogata w cynk składa się z dużej ilości mikrodrobnego proszku cynku i niewielkiej ilości materiałów błonotwórczych. Właściwości elektrochemiczne cynku są wyższe niż stali, a poddawany korozji wykazuje działanie „samopoświęcające”, dzięki czemu stal jest chroniona. Produkt korozji, tlenek cynku, wypełnia pory i sprawia, że powłoka jest bardziej gęsta. Powszechnie stosowany podkład bogaty w cynk ma następujące trzy rodzaje:
(1) nieorganiczny podkład bogaty w cynk ze szkła wodnego, jest to szkło wodne jako materiał bazowy, dodać proszek cynkowy, wymieszać i szczotkować, po utwardzeniu spłukać wodą, proces budowy jest złożony, trudne warunki procesu, obróbka powierzchni musi być w Sa2,5 lub więcej, oprócz wymagań dotyczących temperatury otoczenia i wilgotności, tworzenie się powłoki jest łatwe do pękania, łuszczenia się i jest rzadko stosowane.
(2) rozpuszczalny nieorganiczny podkład bogaty w cynk, podkład na bazie ortokrzemianu etylu, alkoholu jako rozpuszczalnika, częściowo zhydrolizowana polimeryzacja, dodatek proszku cynkowego wymieszanego równomiernie powlekanego.
(3) podkład bogaty w cynk, jest to żywica epoksydowa jako materiał bazowy tworzący powłokę, z dodatkiem proszku cynkowego, utwardzanie w celu utworzenia powłoki. Podkład epoksydowy bogaty w cynk to nie tylko doskonałe właściwości antykorozyjne i silna przyczepność, a przy kolejnej powłoce farby epoksydowo-żelazowo-chmurowe mają dobry typ przyczepności. Stosowany głównie w ogólnej atmosferze stalowej konstrukcji ramy i korozji urządzeń petrochemicznych.
Podkład epoksydowy czerwony tlenek żelaza dzieli się na puszki z farbą dwuskładnikową, składnik A (farba) wykonany z żywicy epoksydowej, czerwonego tlenku żelaza i innych pigmentów antykorozyjnych, środek utwardzający, środek przeciw zatapianiu itp., składnik B jest utwardzaczem, konstrukcja proporcji rozmieszczenia. Czerwony tlenek żelaza jest rodzajem fizycznego pigmentu antykorozyjnego, jego natura jest stabilna, silna siła krycia, drobne cząstki, może odgrywać dobry efekt ekranowania w warstwie farby, ma dobre działanie antykorozyjne. Podkład epoksydowo-żelazowy czerwony na płycie stalowej i górna warstwa farby epoksydowej mają dobrą przyczepność, szybko schną w temperaturze pokojowej, górna warstwa farby powierzchniowej nie blaknie, częściej stosowana w rurociągach stalowych, zbiornikach, projektach antykorozyjnych konstrukcji stalowych jako podkład rdzy.
4.2 środkowa warstwa farby
Farbą warstwy środkowej jest zazwyczaj mika epoksydowa i farba epoksydowa w postaci łuski szklanej lub farba w postaci gęstej zawiesiny epoksydowej. Farba mikowa epoksydowa jest wytwarzana z żywicy epoksydowej jako materiału podstawowego poprzez dodanie tlenku żelaza miki, mikrostruktura tlenku żelaza miki jest jak łuszcząca się mika, jej grubość wynosi tylko kilka mikrometrów, a jej średnica wynosi od kilkudziesięciu mikrometrów do stu mikrometrów. Jest to odporność na wysoką temperaturę, odporność na alkalia, kwasoodporność, nietoksyczność, struktura płatków może zapobiegać średniej penetracji, zwiększone działanie antykorozyjne i niski skurcz, chropowatość powierzchni, jest doskonałą środkową warstwą farby antykorozyjnej. Farba epoksydowa z łuską szklaną składa się z żywicy epoksydowej jako materiału podstawowego, z łuszczącą się zgorzeliną szklaną jako kruszywem oraz różnymi dodatkami w postaci grubej farby antykorozyjnej typu łopatkowego. Grubość łuski szkła wynosi tylko 2 do 5 mikronów. Ponieważ łuski ułożone są warstwami powyżej i poniżej powłoki, powstaje unikalna struktura ekranująca.
Warstwa wierzchnia 4.3
Farby stosowane do powłok nawierzchniowych można podzielić na trzy klasy w zależności od ich przedziału cenowego:
(1) Zwykły gatunek to farba epoksydowa, farba chlorokauczukowa, chlorosulfonowany polietylen i tak dalej;
(2) Średniej jakości jest farbą poliuretanową;
(3) Wyższa jakość to farba poliuretanowa modyfikowana silikonem, akrylowa powłoka nawierzchniowa modyfikowana silikonem, farba fluorowa i tak dalej.
Farba epoksydowa po utwardzeniu chemicznym, stabilność chemiczna, gęsta powłoka, silna przyczepność, wysokie właściwości mechaniczne, jest odporna na kwasy, zasady, sól, może wytrzymać różnorodne czynniki korozyjne w mediach chemicznych.
5. Wybór farby antykorozyjnej powinien uwzględniać kilka punktów
5.1 Należy zwrócić uwagę na zgodność warunków użytkowania konstrukcji i wybór farb, w zależności od medium korozyjnego (rodzaj, temperatura i stężenie), fazy gazowej lub fazy ciekłej, obszarów gorących i wilgotnych lub suchych i innych warunki selekcji. W przypadku środowiska kwaśnego można zastosować farbę na bazie żywicy fenolowej o lepszej odporności na kwasy, natomiast w przypadku środowiska zasadowego należy zastosować farbę na bazie żywicy epoksydowej o lepszej odporności na działanie zasad.
5.2 Należy uwzględnić możliwości warunków budowy. Niektóre nadają się do szczotkowania, niektóre nadają się do natryskiwania, inne nadają się do naturalnego suszenia w celu utworzenia filmu i tak dalej. Do warunków ogólnych zaleca się stosowanie suchej, łatwej do natryskiwania farby utwardzającej się na zimno.
5.3 Rozważ właściwe dopasowanie powłok. Ponieważ większość farby to organiczny materiał koloidalny jako materiał bazowy, pomaluj każdą warstwę folii, nieuchronnie istnieje wiele wyjątkowo małych mikroporowatych, a czynniki korozyjne mogą nadal przenikać przez erozję stali. Dlatego też obecnie stosowane konstrukcje farb nie są powlekane jednowarstwowo, lecz wielowarstwowo, celem jest ograniczenie mikroporowatości do minimum. Powinna istnieć dobra zdolność adaptacji pomiędzy podkładem i powłoką nawierzchniową. Takie jak farba z chlorku winylu i podkład fosforanujący lub podkład alkidowy z czerwienią żelazną wspomagający stosowanie dobrych wyników i nie można go stosować z podkładem na bazie oleju (takim jak czerwona farba na bazie oleju) wspomagającym użycie. Ponieważ farba perchloroetylenowa zawiera mocne rozpuszczalniki, zniszczy warstwę podkładu.
Ogromne znaczenie ma wykonanie dobrej roboty w zakresie ochrony antykorozyjnej i antykorozyjnej, aby promować rozwój budownictwa o konstrukcji stalowej, oszczędzać materiały, przedłużać żywotność budynku, zapewniać bezpieczną produkcję i zmniejszać zanieczyszczenie środowiska.
Nr 568, Yanqing First Class Road, Jimo High-Tech Zone, Qingdao City, Shandong Prowince, Chiny
Copyright © 2024 Qingdao Eihe Stal Structure Group Co., Ltd. Wszelkie prawa zastrzeżone.
Links | Sitemap | RSS | XML | Privacy Policy |
Teams